Load Manifests
Standard Operating Procedures
Table of Contents
To enhance our operational efficiency and reduce the errors that have the potential to lead to very significant financial losses, we are introducing load manifests to streamline logistics. By implementing load manifests, we aim to foster greater accountability across all levels of our operations, from employees responsible for preparing transfers, to supervisors overseeing these preparations, and drivers verifying their loads at the end of each day.
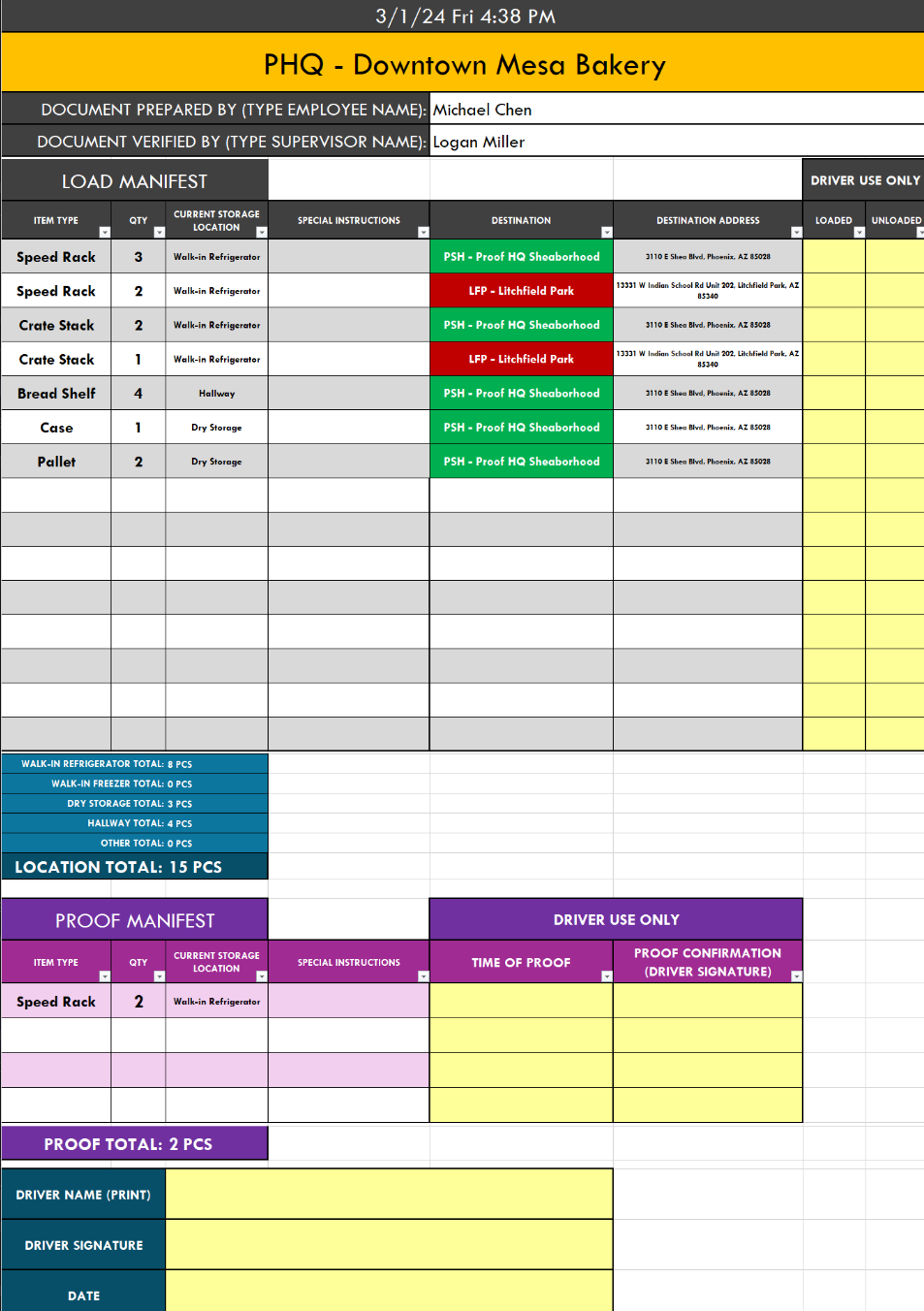
Bakery Managers and Shift Leads
- Staff are expected to fill out the load and proof manifests daily, much like they do now with the current requests system.
- This sheet is already pinned and located on all store computers.
- Staff are required to put their name on the manifest sheet.
- A supervisor (Shift Lead or Bakery Manager) must also enter their name on the sheet verifying that their work is accurate.
- The date and time on the sheet auto-updates to the current time and date automatically.
- There are preset options for item type (e.g. speed rack, bread shelf, pallet, case), current storage location (e.g. walk-in refrigerator, dry storage, hallway), and location that must be entered.
- The colors of the location cells correlate with tape colors placed on the items to be transferred.
- Each label much be written using fractional numbering.
- Each label should correspond with the load manifest total, or the proof manifest total, respectively.
- Items should still have detail regarding par dates and phase dates, if applicable.
- Accurate quantity of each line item must be entered.
- Special instructions can be added for each line item to give certain notes to the drivers when loading those items.
- These load manifests must be finished and printed before 3PM daily at each facility.Â
- Finished manifests must be put inside a sheet protector attached to the proofer door.
Truck Drivers
- Arriving at each facility, the staff will have prepared for you a load manifest that will be attached on the facility's proofer door in a sheet protector.
- Transfer the load manifest onto the clipboard we have assigned you.
- On the sheet, verify that the date matches with today's date.
- Pay attention to the LOCATION TOTAL and PROOF TOTAL and the PCS count to verify you have taken the correct number of pieces from each location and loaded them onto the truck or put them into the proofer. This will ensure you do not miss anything critical.
- Items will be labeled using the color that correlates with its destination, with fractional numbering as well.
- The colors of the location cells correlate with tape colors.
- Pay attention to the yellow highlighted cells, all of which must be completely filled out by the end of your shift.
- Check off boxes in the LOADED column as you load items onto the truck and UNLOADED column as you unload each item at each location for each line item in the load manifest.
- The time that the proof was set and the driver signature must be entered for all line items in the proof manifest.
- The printed name, signature, and date must be filled out upon completing the designated transfer route.
- Only pictures of the completed manifests are necessary with all yellow highlighted cells filled out. The pictures of these completed documents must be sent in the #logistics channel in Discord.
- No other pictures are necessary anymore.
- Finished manifests should be archived in a file organizer at the final destination of the transfer route in a clearly designated location.
What happens to inbound transfer requests?
- Each facility's staff is expected to make phone calls using the facility phones for urgent requests. Refer to the SOP on Communication if necessary.
- Whether or not the request can be fulfilled, the bakery manager should still be informed.
- Bakery managers should put procurement requests in Asana in the Supply Chain Management Project in the Procurement section as tasks assigned to Michael.
Compliance
- Employees: Responsible for adhering to the procedures outlined in this SOP during their daily tasks. This includes preparing, executing, and completing tasks as specified, and reporting any issues or deviations from the SOP to their immediate supervisor.
- Shift Leads and Bakery Managers: Accountable for overseeing the correct implementation of the SOP by employees, providing necessary training, and conducting regular audits to ensure compliance. Supervisors are also responsible for addressing any deviations from the SOP and taking corrective action as needed.
- Systems Director and District Production Manager: Ensure that the SOP is up-to-date, effective, and in alignment with organizational goals. These individuals are also responsible for reviewing audit reports, addressing systemic issues, and making decisions on updates to the SOP based on feedback and changing operational needs.
- Failure to accommodate any step as outlined in this SOP that can be deemed to be the root cause of a significant financial loss, as determined by senior management, can result in disciplinary action, up to and including immediate termination.
Â